Plastik atıklar, günümüzde çevresel sorunların önemli bir kaynağı haline gelmiştir. Bu atıkların doğada yıllarca parçalanmadan kalabilmesi ve çevreye verdiği zararlar, plastik geri dönüşümünün önemini artırmaktadır. Plastik geri dönüşüm teknolojileri, atık plastik malzemelerin yeniden kullanılabilir hale getirilerek çevreye olan etkisini azaltmayı hedefler.
Plastik geri dönüşümü, atık plastik malzemelerin toplanması, ayrıştırılması, temizlenmesi ve yeniden işlenmesi sürecini içerir. İlk adım, atık plastiklerin doğru bir şekilde toplanmasıdır. Bu, geri dönüşüm için ayrılmış konteynerlerin kullanılması veya geri dönüşüm merkezlerine atıkların teslim edilmesiyle gerçekleştirilebilir.
Toplanan plastik atıklar, geri dönüşüm tesislerine gönderilerek ayrıştırma işlemine tabi tutulur. Ayrıştırma, farklı plastik türlerini birbirinden ayırma işlemidir. Plastikler genellikle polietilen tereftalat (PET), polietilen (PE), polipropilen (PP), polivinilklorür (PVC) ve polistiren (PS) gibi farklı türlerde bulunur. Bu türlerin ayrıştırılması, daha etkili bir geri dönüşüm süreci için önemlidir.
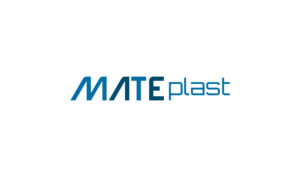
Ayrıştırma işleminden sonra, plastikler temizlenir. Atıkların üzerindeki kirleticiler, etiketler ve kaplamalar çıkarılır. Plastiklerin temizlenmesi, geri dönüşüm işlemi için önemlidir çünkü kirlilik, geri dönüşüm sırasında kaliteyi olumsuz etkileyebilir.
Temizlenen plastik malzemeler, geri dönüşüm tesisinde öğütülerek granüller haline getirilir. Bu granüller daha sonra farklı plastik ürünlerin üretiminde kullanılabilir. Örneğin, PET plastik granülleri, şişe ve gıda ambalajları gibi ürünlerin üretiminde kullanılabilir.
Bazı plastikler, termoplastik özellik gösterir. Bu tür plastikler, ısıtıldığında yeniden şekillendirilebilir. Geri dönüşüm tesislerinde, termoplastik plastiklerin eritilip yeniden şekillendirilmesi işlemi gerçekleştirilir. Eritilen plastik malzeme, özel kalıplara enjekte edilerek yeni plastik ürünlerin üretiminde kullanılır. Bu süreç, geri dönüşümü mümkün kılan döngüsel bir ekonomi modeli olan “kaynağa dayalı geri dönüşüm”ün bir örneğidir.
Plastik geri dönüşüm teknolojileri sürekli gelişmektedir. Yenilikçi yöntemler ve ileri teknolojiler, plastik atıkların geri dönüşümünde daha verimli ve etkili sonuçlar sağlamaktadır. Örneğin, bazı tesislerde kimyasal geri dönüşüm yöntemleri kullanılarak plastik atıklar moleküler seviyede parçalanır ve daha sonra yeniden sentezlenerek yeni plastik ürünlerin üretiminde kullanılır. Bu yöntem, karmaşık ve karmaşık yapılı plastiklerin geri dönüşümünü mümkün kılar.
Plastik geri dönüşümünün önemli faydaları vardır. İlk olarak, atık plastik malzemelerin geri dönüşümü, doğal kaynakların korunmasına yardımcı olur. Yeni plastik üretimi için gereken petrol ve doğal gaz gibi kaynakların tüketimini azaltır. Ayrıca, plastik atıkların doğada çöp olarak birikmesini engelleyerek çevre kirliliğini önler.
Plastik geri dönüşümü, enerji tasarrufu sağlar. Plastiklerin geri dönüştürülmesi, ham plastik üretimine göre daha az enerji gerektirir. Bu da enerji kaynaklarının daha verimli kullanılmasını sağlar.
Ayrıca, plastik geri dönüşümü ekonomik faydalar sağlar. Geri dönüşüm sektörü, istihdam yaratır ve ekonomiye katkıda bulunur. Geri dönüştürülen plastik malzemeler, yeniden kullanılabilir hale getirilerek yeni ürünlerin üretiminde kullanılır ve bu da ekonomik değer yaratır.
Sonuç olarak, plastik geri dönüşüm teknolojileri çevresel sorunların azaltılmasında önemli bir rol oynamaktadır. Doğru bir şekilde toplanan, ayrıştırılan, temizlenen ve yeniden işlenen plastik atıklar, doğal kaynakların korunmasına, enerji tasarrufuna ve ekonomik faydalara katkıda bulunur. Bireyler olarak, plastik atıkların geri dönüşümüne destek olmak ve bu konuda bilinçli tüketici alışkanlıkları geliştirmek, daha sürdürülebilir bir gelecek için önemlidir.
Mekanik Geri Dönüşüm: Plastiklerin Kırılması ve İşlenmesi
Plastik geri dönüşümü, atık plastik malzemelerin çevreye olan etkisini azaltmak amacıyla yeniden kullanılabilir hale getirilmesini sağlar. Plastiklerin mekanik geri dönüşümü, bu sürecin en yaygın ve temel yöntemlerinden biridir.
Mekanik geri dönüşüm, plastik atıkların fiziksel olarak kırılması ve işlenmesi yoluyla gerçekleştirilir. İşlem genellikle aşağıdaki adımları içerir:
Toplama ve Ayırma: İlk adım, plastik atıkların doğru bir şekilde toplanması ve ayrıştırılmasıdır. Plastik malzemelerin farklı türleri, örneğin PET, PE, PP gibi, ayrı konteynerlere veya geri dönüşüm tesislerine yönlendirilir. Bu aşamada, plastiklerin diğer malzemelerden, örneğin metal veya kağıttan, ayrıştırılması da gerçekleştirilir.
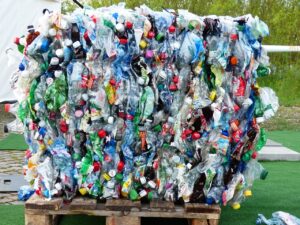
Kırma ve Öğütme: Toplanan plastik atıklar, özel ekipmanlar kullanılarak kırılır ve öğütülür. Plastiklerin boyutu küçültülerek granüller veya pullar elde edilir. Bu işlem, plastik malzemelerin daha kolay işlenebilir hâle gelmesini sağlar.
Yıkama ve Temizleme: Kırılan plastik malzemeler, temizlenmek ve kirleticilerden arındırılmak için yıkama işlemine tabi tutulur. Bu aşamada, plastikler üzerindeki etiketler, kaplamalar ve kirleticiler çıkarılır. Temizlenen plastik malzemeler, daha ileri işleme adımlarında kullanılmak üzere hazırlanır.
Kurutma: Yıkama işleminden sonra, plastik malzemeler kurutulur. Nem, geri dönüşüm sürecinde istenmeyen etkiler yaratabileceğinden, kurutma önemli bir adımdır. Plastiklerin kurutulması, daha verimli bir işleme süreci sağlar.
İşleme ve Ekstrüzyon: Kurutulan plastik malzemeler, ekstrüzyon adı verilen bir işlemle eritilir. Plastik granülleri veya pulları, ısı ve basınç altında eritilerek plastik hamuru haline getirilir. Bu hamur, daha sonra şekillendirme işlemleri için kullanılan özel kalıplara enjekte edilir veya ekstrüzyon işlenir. Ekstrüzyon işlemi, plastik malzemenin bir kalıptan geçirilerek istenilen şekli almasını sağlar. Bu şekillendirme işlemiyle, geri dönüştürülmüş plastiklerin yeni ürünlerin üretiminde kullanılması mümkün hale gelir.
Ürünleştirme: Ekstrüzyon işlemi sonucunda elde edilen plastik hamuru, çeşitli üretim yöntemleriyle şekillendirilebilir. Bu plastik malzemeler, enjeksiyon kalıplama, döküm, şişirme veya ekstrüzyon yöntemleriyle farklı plastik ürünlerin üretiminde kullanılabilir. Örneğin, geri dönüştürülmüş plastik malzemeler, yeni ambalaj ürünleri, kaplar, borular veya levhalar gibi çeşitli endüstriyel ve tüketici ürünlerinin imalatında kullanılabilir.
Mekanik geri dönüşüm yöntemi, plastik atıkların geri dönüşümü için etkili ve yaygın olarak kullanılan bir yöntemdir. Bu yöntemin bazı avantajları vardır. İlk olarak, mekanik geri dönüşüm süreci enerji tasarrufu sağlar. Plastiklerin eritilmesi için gereken enerjiden daha az enerji kullanılır, bu da kaynakların daha verimli kullanılmasını sağlar. Ayrıca, mekanik geri dönüşüm, çevrede daha az atık oluşmasına yardımcı olur ve doğal kaynakların korunmasına katkıda bulunur.
Bununla birlikte, mekanik geri dönüşümün bazı sınırlamaları da vardır. Örneğin, plastiklerin tekrar tekrar geri dönüştürülmesiyle malzemenin kalitesi zamanla azalabilir. Ayrıca, bazı plastik türleri, mekanik geri dönüşüm süreci için uygun olmayabilir ve kimyasal geri dönüşüm yöntemlerinin kullanılması gerekebilir.
Sonuç olarak, mekanik geri dönüşüm, plastik atıkların yeniden kullanılabilir hale getirilmesi için yaygın olarak kullanılan bir yöntemdir. Plastiklerin kırılması, işlenmesi, temizlenmesi ve yeniden şekillendirilmesiyle, plastik atıkların çevreye olan etkisi azaltılarak kaynakların korunması sağlanır. Mekanik geri dönüşüm, plastik atıkların sürdürülebilir bir şekilde yönetilmesine ve döngüsel bir ekonomi modelinin oluşturulmasına önemli bir katkı sağlar.
Kimyasal Geri Dönüşüm: Plastiklerin Parçalanması ve Kimyasal Dönüşümü
Kimyasal geri dönüşüm, plastik atıkların parçalanması ve kimyasal dönüşümü yoluyla gerçekleştirilen bir geri dönüşüm yöntemidir. Bu yöntem, karmaşık ve karmaşık yapılı plastiklerin geri dönüşümünü mümkün kılar.
Kimyasal geri dönüşüm süreci, plastik atıkların moleküler seviyede parçalanmasını ve daha sonra bu parçalanmış moleküllerin yeniden sentezlenerek yeni plastik ürünlerin üretiminde kullanılmasını içerir. Bu süreç, genellikle aşağıdaki adımları içerir:
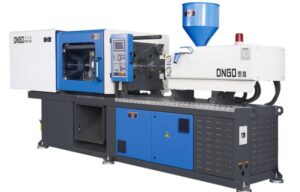
Parçalanma: Plastik atıklar, özel kimyasal işlemler veya termal işlemler kullanılarak parçalanır. Kimyasal geri dönüşümde yaygın olarak kullanılan yöntemlerden biri, plastikleri parçalamak için kullanılan kimyasal çözücülerin veya reaktiflerin kullanılmasıdır. Bu çözücüler veya reaktifler, plastikleri moleküler seviyede ayırarak daha küçük parçalara dönüştürür.
Kimyasal Dönüşüm: Parçalanan plastik molekülleri, kimyasal reaksiyonlar yoluyla yeniden sentezlenir. Bu aşamada, parçalanan moleküllerin kimyasal yapısı değiştirilir ve yeni plastik malzemelerin üretiminde kullanılmak üzere uygun hale getirilir. Kimyasal dönüşüm işlemi, plastik atıkların farklı plastik türlerine dönüştürülmesini sağlar, böylece daha geniş bir ürün yelpazesinde kullanılabilir hale gelir.
Arıtma ve Raffinasyon: Kimyasal dönüşüm sürecinden elde edilen plastik malzemeler, arıtma ve raffinasyon adımlarından geçirilir. Bu adımlar, istenmeyen katkı maddelerinin, kirleticilerin ve yan ürünlerin uzaklaştırılmasını sağlar. Plastik malzemelerin kalitesini artırarak, yeni plastik ürünlerin üretiminde kullanılmak üzere uygun hale gelir.
Ürünleştirme: Kimyasal geri dönüşüm süreci sonucunda elde edilen plastik malzemeler, farklı üretim yöntemleri kullanılarak şekillendirilebilir. Enjeksiyon kalıplama, ekstrüzyon, dökme veya diğer yöntemler kullanılarak plastik malzemeler istenilen şekillerde ürünleştirilir. Bu üretim yöntemleri, geri dönüştürülmüş plastiklerin yeni ambalaj malzemeleri, plastik kaplar, oyuncaklar, otomotiv parçaları ve daha birçok ürünün üretiminde kullanılmasını sağlar.
Kimyasal geri dönüşümün birkaç avantajı vardır. İlk olarak, bu yöntem karmaşık ve karmaşık yapılı plastiklerin geri dönüşümünü mümkün kılar. Mekanik geri dönüşüm yöntemiyle işlenmesi zor olan plastik türleri, kimyasal geri dönüşümle yeniden kullanılabilir hale getirilebilir. İkincisi, kimyasal geri dönüşüm süreci, plastik atıkların tekrar tekrar geri dönüştürülmesini sağlar, bu da malzemenin ömrünü uzatır ve kaynakların daha etkin bir şekilde kullanılmasını sağlar. Üçüncüsü, kimyasal geri dönüşüm, daha düşük enerji tüketimi gerektiren bir süreçtir. Plastiklerin parçalanması ve kimyasal dönüşümü için gerekli enerji miktarı, ham plastik üretimine kıyasla daha düşüktür.
Ancak, kimyasal geri dönüşüm yöntemi de bazı zorluklarla karşılaşabilir. İlk olarak, kimyasal geri dönüşüm süreci daha karmaşık ve maliyetli olabilir. Özel kimyasal reaktiflerin kullanılması, işlem maliyetini artırabilir. İkincisi, bu yöntemle geri dönüştürülen plastik malzemelerin kalitesi, mekanik geri dönüşümle elde edilenlerden daha düşük olabilir. Bu nedenle, kimyasal geri dönüşüm genellikle yüksek kaliteli ürünlerin üretiminde tercih edilir.
İstatistik | Değer |
---|---|
Küresel Plastik Geri Dönüşüm Pazar Değeri (2023) | 52.07 Milyar USD |
Tahmini Küresel Plastik Geri Dönüşüm Pazar Değeri (2028) | 74.3 Milyar USD |
Bileşik Yıllık Büyüme Oranı (CAGR) | %7.3 |
Sonuç olarak, kimyasal geri dönüşüm, plastik atıkların parçalanması ve kimyasal dönüşümü yoluyla geri dönüştürülmesini sağlayan bir yöntemdir. Bu yöntem, karmaşık plastik malzemelerin geri dönüşümünü mümkün kılar ve plastik atıkların daha geniş bir ürün yelpazesinde kullanılmasını sağlar. Kimyasal geri dönüşüm, plastik atıkların sürdürülebilir bir şekilde yönetilmesi ve kaynakların daha verimli kullanılması için önemli bir adımdır.
Biyolojik Geri Dönüşüm: Plastiklerin Biyolojik olarak Parçalanması
Biyolojik geri dönüşüm, plastik atıkların doğal olarak parçalanması ve biyolojik süreçler aracılığıyla geri dönüştürülmesi anlamına gelir. Bu yöntem, plastik atıkların çevresel etkisini azaltmak ve sürdürülebilir bir atık yönetimi sağlamak amacıyla kullanılan önemli bir geri dönüşüm yöntemidir.
Biyolojik geri dönüşüm süreci, mikroorganizmalar ve enzimler aracılığıyla gerçekleşir. Plastik atıkların biyolojik olarak parçalanabilmesi için genellikle aşağıdaki adımlar izlenir:
Biyolojik Ayrışma: Plastik atıklar, özellikle biyobozunur plastikler, doğal çevrede bulunan mikroorganizmaların ve enzimlerin etkisiyle ayrışmaya başlar. Bu mikroorganizmalar, plastikleri parçalayabilen enzimleri salgılar ve plastik moleküllerini daha küçük parçalara ayırır.
Biyolojik Dönüşüm: Parçalanan plastik parçacıkları, mikroorganizmalar tarafından kullanılarak enerji ve besin kaynaklarına dönüştürülür. Bu süreçte, mikroorganizmalar plastik parçacıklarını besin olarak kullanır ve bunları metabolize eder. Plastik molekülleri, mikroorganizmaların büyümesi ve çoğalması için gerekli enerjiyi sağlamak üzere kullanılır.
Kompostlaşma veya Fermentasyon: Biyolojik olarak parçalanan plastik atıklar, kompostlaşma veya fermantasyon gibi doğal süreçlerle daha da ayrışır. Bu süreçte, plastik parçacıkları doğal toprak ortamına dönüşür ve organik madde içeren toprak bileşimine katkıda bulunur. Bu süreç sonucunda elde edilen kompost veya fermente malzemeler, tarım veya bahçecilik gibi alanlarda kullanılabilir.
Biyolojik geri dönüşüm yönteminin bazı avantajları vardır. Öncelikle, doğal çevrede plastiklerin biyolojik olarak parçalanması, çevresel etkilerin azalmasına katkıda bulunur. Plastik atıkların doğal olarak ayrışması, kirlilik riskini azaltır ve ekosisteme zarar veren uzun ömürlü plastik atıkların miktarını azaltır. İkinci olarak, biyolojik geri dönüşüm süreci genellikle daha az enerji tüketir. Kimyasal veya termal işlemler gerektirmeyen bu yöntem, enerji tasarrufu sağlar ve çevresel açıdan daha sürdürülebilir bir seçenektir.
Ancak, biyolojik geri dönüşüm yöntemi de bazı zorluklarla karşılaşabilir. Öncelikle, biyolojik olarak parçalanabilen plastiklerin kullanımı yaygın değildir. Birçok plastik türü, biyolojik olarak ayrışabilme özelliğine sahip değildir ve bu nedenle biyolojik geri dönüşüm için uygun değildir. İkincisi, biyolojik geri dönüşüm süreci zaman alabilir. Plastiklerin biyolojik olarak parçalanması ve ayrışması doğal süreçler gerektirdiğinden, geri dönüşüm süreci uzun olabilir.
Biyolojik geri dönüşüm, plastik atıkların sürdürülebilir bir şekilde yönetilmesine yardımcı olan önemli bir yöntemdir. Bu yöntem, doğal çevrede plastiklerin parçalanmasını ve ayrışmasını teşvik ederek atık miktarını azaltır. Plastik üreticileri ve tüketicileri, biyolojik olarak parçalanabilen plastiklere yönelik tercihlerini artırarak biyolojik geri dönüşüm sürecini destekleyebilirler. Ayrıca, biyolojik geri dönüşüm araştırmalarına ve teknolojilere yatırım yapmak, bu yöntemin etkinliğini ve uygulanabilirliğini artırabilir.
Sonuç olarak, biyolojik geri dönüşüm plastik atıkların doğal süreçlerle parçalanması ve dönüştürülmesi yöntemidir. Bu yöntem, çevresel etkileri azaltır, enerji tasarrufu sağlar ve sürdürülebilir bir atık yönetimi için önemli bir adımdır. Biyolojik geri dönüşüm, plastik atıkların çevreye olan zararını en aza indirmek ve doğal kaynakların korunmasına katkıda bulunmak için önemli bir çözümdür.
Enerji Kazanımı: Plastiklerin Enerji Üretimi İçin Kullanılması
Plastik atıkların enerji kazanımı, atıkların yakılması veya termal işlemlerle enerji üretimi için kullanılması anlamına gelir. Bu yöntem, plastik atıkların çevreye olan etkisini azaltmak ve atık yönetimi için enerji kaynaklarını kullanmak amacıyla uygulanan bir geri dönüşüm yöntemidir.
Plastiklerin enerji üretimi için kullanılması genellikle atık yakma tesislerinde veya enerji geri kazanım tesislerinde gerçekleşir. Bu süreç genellikle şu adımları içerir:
Toplama ve Ayrıştırma: Plastik atıklar, geri dönüşüm tesislerine toplanır ve uygun şekilde ayrıştırılır. Plastikler, diğer atık malzemelerden ayrılır ve enerji üretimi için kullanılmak üzere ayrı bir işleme tabi tutulur.
Yakma veya Termal İşlem: Plastik atıklar, yakma veya termal işlem adı verilen süreçlerle enerji üretimi için kullanılır. Yakma işlemi, plastikleri yüksek sıcaklıklarda yakarak enerji üretir. Bu enerji, elektrik veya ısı olarak kullanılabilir. Termal işlem ise plastikleri yüksek sıcaklıklarda eriterek enerji üretimini sağlar.
Enerji Geri Kazanımı: Plastiklerin yakılması veya termal işlemi sonucunda elde edilen enerji, elektrik üretimi veya ısınma gibi enerji ihtiyaçlarında kullanılır. Bu enerji, elektrik şebekesine bağlı tesislerde elektrik üretmek için kullanılabilir veya ısıtma sistemlerinde enerji kaynağı olarak değerlendirilebilir.
Plastiklerin enerji üretimi için kullanılmasının bazı avantajları vardır. İlk olarak, bu yöntem, plastik atıkların çevreye olan etkisini azaltır. Atık plastiklerin enerjiye dönüştürülerek yakılması veya termal işleme tabi tutulması, atıkların doğal çevreye yayılmasını önler ve çevresel kirliliği azaltır. İkincisi, plastik atıklardan elde edilen enerji, enerji kaynaklarının kullanımını çeşitlendirir. Plastik atıklar enerji olarak kullanıldığında, diğer enerji kaynaklarına olan talep azalır ve enerji tüketiminde çeşitlilik sağlanır.
Ancak, plastiklerin enerji üretimi için kullanılması yöntemi bazı zorluklar yaratabilir. İlk olarak, plastiklerin yanması veya termal işleme tabi tutulması sırasında çevreye zararlı gazlar ve kirleticiler açığa çıkabilir. Bu nedenle, atık yakma tesislerinin ve enerji geri kazanım tesislerinin uygun filtreleme ve arıtma sistemlerine sahip olması önemlidir. İkinci olarak, plastiklerin enerji üretimi için kullanılması, geri dönüşüm veya yeniden kullanım gibi daha sürdürülebilir seçeneklere öncelik verme eğiliminde olmaktadır. Plastik atıkların enerji üretimi için kullanılması, atıkların tekrar kullanılabilir veya geri dönüştürülebilir potansiyelini azaltabilir.
Plastik atıkların enerji üretimi için kullanılması, atık yönetimi stratejilerinde bir seçenek olarak değerlendirilmelidir. Ancak, bu yöntem, diğer geri dönüşüm ve atık azaltma yöntemleriyle birlikte kullanılmalıdır. Öncelik, plastik atıkların geri dönüşümüne, yeniden kullanımına ve azaltılmasına verilmelidir. Plastiklerin enerji üretimi için kullanılması, geri dönüşümün mümkün olmadığı veya uygun olmadığı durumlarda bir alternatif olabilir.
Sonuç olarak, plastik atıkların enerji kazanımı yöntemi, atıkların enerji üretimi için kullanılmasını sağlar. Bu yöntem, çevreye olan etkiyi azaltırken enerji kaynaklarının kullanımını çeşitlendirir. Ancak, atık yakma veya termal işlem sürecinde ortaya çıkan çevresel etkiler ve sürdürülebilirlik açısından diğer seçeneklerle birlikte değerlendirilmelidir. Plastik atıkların enerji üretimi için kullanılması, atık yönetimi stratejilerinde bir bileşen olabilir, ancak atık azaltma, geri dönüşüm ve yeniden kullanım gibi sürdürülebilir seçeneklere öncelik verilmesi gerekmektedir.
Gelişmiş Geri Dönüşüm Teknolojileri ve Yenilikler
Geri dönüşüm teknolojileri, plastik atıkların daha etkili bir şekilde geri dönüştürülmesi için sürekli olarak geliştirilmektedir. Yenilikçi yaklaşımlar ve ileri teknolojiler, atık yönetimi sektöründe önemli ilerlemeler kaydetmekte ve plastik atıkların sürdürülebilir bir şekilde değerlendirilmesini sağlamaktadır.
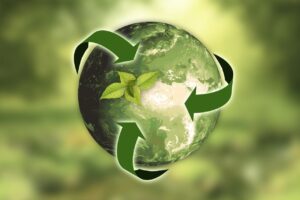
Kimyasal Geri Dönüşüm: Kimyasal geri dönüşüm, plastik atıkların kimyasal işlemlerle parçalanması ve daha sonra bu parçalardan yeni plastik üretimi yapılmasıdır. Bu yöntem, geleneksel mekanik geri dönüşüm yöntemlerinin yetersiz kaldığı plastik türleri için idealdir. Kimyasal geri dönüşüm, plastik atıkları polimerlerine ayırarak orijinal kalitelerine yakın yeni plastik üretimine olanak sağlar.
Biyolojik Fermentasyon: Biyolojik fermantasyon, mikroorganizmaların plastik atıkları doğal olarak parçalayarak enerji üretimi için kullanmasıdır. Bu yöntemde, mikroorganizmalar plastikleri metabolize ederek biyogaz veya biyodizel gibi enerji kaynakları üretebilir. Biyolojik fermantasyon, biyolojik geri dönüşümün bir türüdür ve sürdürülebilir enerji üretimine katkıda bulunur.
İleri Ayırma Teknolojileri: Plastik atıkların etkili bir şekilde geri dönüştürülmesi için gelişmiş ayırma teknolojileri kullanılmaktadır. Optik ayırma sistemleri, manyetik ayırıcılar ve yakıt analiz cihazları gibi teknolojiler, plastikleri farklı türlerine ve bileşenlerine ayırmak için kullanılır. Bu yöntemler, geri dönüşüm sürecini daha verimli hâle getirir ve plastiklerin daha yüksek kaliteli geri dönüşüm malzemelerine dönüştürülmesini sağlar.
Plastik Yeniden Tasarımı: Plastik atıkların azaltılması için plastik yeniden tasarımı da önemli bir yaklaşımdır. Bu, plastik üreticilerinin daha çevre dostu ve geri dönüştürülebilir plastik malzemeler geliştirmelerini içerir. Örneğin, biyobozunur plastikler veya yeniden kullanılabilir ambalajlar gibi alternatif malzemelerin kullanımı, plastik atıkları azaltmaya yardımcı olur. Plastik yeniden tasarımı, plastik ürünlerin ömrünü uzatmak ve geri dönüşüm potansiyelini artırmak için malzeme seçiminden ürün tasarımına kadar bir dizi faktörü içerir.
Nanoteknoloji Uygulamaları: Nanoteknoloji, plastik geri dönüşümünde önemli bir yenilikçi alan olarak ortaya çıkmaktadır. Nanomalzemeler, plastiklerin mekanik özelliklerini ve geri dönüşüm kabiliyetini artırabilir. Örneğin, nanopartiküllerin eklenmesiyle plastiklerin dayanıklılığı ve esnekliği artabilir, geri dönüşüm süreci daha etkili hale gelebilir ve geri dönüştürülen malzemelerin kalitesi iyileştirilebilir.
Akıllı Geri Dönüşüm Sistemleri: İnternet of Things (IoT) teknolojisi ve sensörlerin kullanımıyla akıllı geri dönüşüm sistemleri geliştirilmektedir. Bu sistemler, plastik atıkların toplanması, ayrıştırılması ve geri dönüştürülmesi sürecini optimize eder. Sensörler, atık miktarını izler, geri dönüşüm konteynerlerinin doluluk oranını bildirir ve verileri analiz ederek atık yönetimi sürecini iyileştirmeye yardımcı olur.
Gelişmiş geri dönüşüm teknolojileri ve yenilikler, plastik atıkların etkili bir şekilde geri dönüştürülmesini sağlamak için önemli bir rol oynamaktadır. Bu teknolojiler, atık yönetimi sürecini daha verimli, çevre dostu ve sürdürülebilir hale getirir. Plastik endüstrisi, yenilikçi yaklaşımlar ve teknolojileri benimseyerek plastik atıkların azaltılması, geri dönüşümü ve dönüştürülmesi konularında önemli adımlar atmaktadır.
Sonuç olarak, gelişmiş geri dönüşüm teknolojileri ve yenilikler, plastik atıkların yönetimi için umut verici çözümler sunmaktadır. Kimyasal geri dönüşüm, biyolojik fermantasyon, ileri ayırma teknolojileri, plastik yeniden tasarımı, nanoteknoloji uygulamaları ve akıllı geri dönüşüm sistemleri gibi yaklaşımlar, plastik atıkların sürdürülebilir bir şekilde değerlendirilmesini sağlar. Bu teknolojilerin yaygınlaşması, plastik atıkların çevreye olan etkisini azaltacak ve döngüsel bir ekonomi için önemli bir adım olacaktır. Araştırmacılar, endüstri liderleri ve hükümetler, gelişmiş geri dönüşüm teknolojilerini teşvik etmek ve yaygınlaştırmak için çalışmaktadır.
Bu yeniliklerin önemi, plastik atıkların küresel çevre sorununa sağladığı çözümlerde yatmaktadır. Plastik atıkların doğaya karışması, su kaynaklarını kirletmesi, deniz ve karasal ekosistemlere zarar vermesi gibi sorunlarla karşı karşıyayız. Gelişmiş geri dönüşüm teknolojileri, plastik atıkların çevreye olan zararını azaltırken, sınırlı kaynakların daha verimli kullanılmasına ve sera gazı emisyonlarının azaltılmasına da katkıda bulunur.
Bununla birlikte, gelişmiş geri dönüşüm teknolojilerinin yaygınlaştırılması ve uygulanması için bazı zorluklar vardır. Bu teknolojilerin maliyetleri yüksek olabilir ve altyapı ve işletme gereksinimleriyle ilgili zorluklar ortaya çıkabilir. Bununla birlikte, bu zorluklar, ilgili paydaşların işbirliği ve yatırım yapma iradesi ile aşılabilecek potansiyele sahiptir.
Gelişmiş geri dönüşüm teknolojilerinin başarılı bir şekilde uygulanması, sürdürülebilir bir gelecek için önemlidir. Plastik atıkların etkin bir şekilde geri dönüştürülmesi, doğal kaynakların korunmasına ve çevre üzerindeki baskının azaltılmasına yardımcı olur. Ayrıca, ekonomik faydalar da sağlar. Geri dönüşüm sektörü istihdam yaratır, yeni iş fırsatları sunar ve ekonomik büyümeyi teşvik eder.
Sonuç olarak, gelişmiş geri dönüşüm teknolojileri ve yenilikler, plastik atıkların etkili bir şekilde yönetilmesi ve sürdürülebilir bir gelecek için önemli bir adımdır. Kimyasal geri dönüşüm, biyolojik fermantasyon, ileri ayırma teknolojileri, plastik yeniden tasarımı, nanoteknoloji uygulamaları ve akıllı geri dönüşüm sistemleri gibi yenilikçi yaklaşımlar, plastik atıkların geri dönüştürülmesini kolaylaştırırken çevre üzerindeki etkisini azaltır. Bu teknolojilerin benimsenmesi ve yaygınlaştırılması, sürdürülebilir bir plastik döngüsü için önemli bir adımdır ve çevre sorunlarıyla mücadele etmek için kritik bir rol oynamaktadır.
Gelecekte, gelişmiş geri dönüşüm teknolojilerinin daha da geliştirilmesi ve yaygınlaştırılması beklenmektedir. Araştırmalar, yeni yöntemlerin ve işlemlerin keşfedilmesiyle birlikte, plastik atıkların daha verimli bir şekilde geri dönüştürülmesini sağlayacak yenilikçi çözümler sunmaktadır. Bununla birlikte, bu teknolojilerin başarılı bir şekilde uygulanabilmesi için, çeşitli paydaşlar arasında işbirliği ve destek önemlidir.
Gelişmiş geri dönüşüm teknolojileri ve yenilikler, sadece plastik atıkların yönetimiyle ilgili değil, aynı zamanda sürdürülebilir bir ekonomi ve toplumun oluşturulmasıyla da ilgilidir. Plastik atıkların geri dönüştürülmesi, doğal kaynakların tükenmesini önler, enerji tasarrufu sağlar ve karbondioksit salınımını azaltır. Ayrıca, geri dönüştürülmüş plastiklerin kullanımı, yeni ürünlerin üretilmesi için daha sürdürülebilir bir kaynak sağlar.
Gelişmiş geri dönüşüm teknolojileri ve yeniliklerin yaygınlaşması için farkındalığın artırılması da önemlidir. Toplumun plastik atıkların etkileri konusunda bilinçlenmesi ve geri dönüşüm süreçlerine katkıda bulunması gerekmektedir. Ayrıca, hükümetler ve endüstri liderleri tarafından teşvik ve düzenlemelerle desteklenen politikaların oluşturulması da bu teknolojilerin yaygınlaşmasına yardımcı olacaktır.
Gelişmiş geri dönüşüm teknolojileri ve yenilikler, plastik atıkların yönetimi ve sürdürülebilirlik hedefleri için umut verici bir yol sunmaktadır. İleri teknolojiler, daha verimli geri dönüşüm süreçleri, çevre dostu ürünler ve ekonomik faydalar sağlayarak plastik atıkların azaltılması ve geri dönüşümü konusunda önemli bir adım oluşturmaktadır.
Sonuç olarak, gelişmiş geri dönüşüm teknolojileri ve yenilikler, plastik atıkların etkili bir şekilde yönetilmesi ve sürdürülebilir bir gelecek için kritik bir rol oynamaktadır. Bu teknolojilerin yaygınlaşması, çevresel etkilerin azaltılması, doğal kaynakların korunması ve ekonomik faydaların elde edilmesi açısından büyük önem taşımaktadır. Gelişmiş geri dönüşüm teknolojileri ve yenilikler, atık yönetimi süreçlerini daha verimli hale getirirken, plastik atıkların yeniden kullanımını ve dönüşümünü teşvik eder.
Bununla birlikte, gelişmiş geri dönüşüm teknolojilerinin yaygınlaşması için bazı zorluklar ve engeller bulunmaktadır. Teknolojik gelişim ve yatırım gerektiren bu süreçlerin maliyeti yüksek olabilir. Altyapı eksiklikleri ve kaynakların sınırlı olması da uygulama sürecini etkileyebilir. Bu nedenle, bu teknolojilerin benimsenmesi için devletler, şirketler ve toplumun genel olarak destekleyici politikalar ve teşvikler geliştirmesi gerekmektedir.
Gelişmiş geri dönüşüm teknolojileri ve yenilikler, plastik atıkların yönetimi konusunda önemli faydalar sunmaktadır. Bunlar arasında enerji tasarrufu, doğal kaynakların korunması, çevre kirliliğinin azaltılması ve iklim değişikliği ile mücadelede etkin bir rol oynama gibi faktörler bulunur. Aynı zamanda, geri dönüşüm süreçlerinin geliştirilmesi ve yaygınlaştırılması, iş fırsatları ve yeşil ekonomi için yeni alanlar yaratır.
Gelişmiş geri dönüşüm teknolojileri ve yeniliklerin geleceği umut vericidir. Araştırmalar ve yenilikler, atık yönetimi süreçlerinin daha etkin ve sürdürülebilir hale getirilmesi için sürekli olarak devam etmektedir. Plastik atıkların yönetimi ve geri dönüşümü konusunda daha fazla bilinç oluşturulması, toplumun bu teknolojilere olan talebini artırabilir ve daha fazla yatırımın yapılmasını sağlayabilir.
Sonuç olarak, gelişmiş geri dönüşüm teknolojileri ve yenilikler, plastik atıkların etkili bir şekilde yönetilmesi ve sürdürülebilir bir gelecek için kritik bir rol oynamaktadır. Bu teknolojilerin yaygınlaşması, atık yönetimi süreçlerinin iyileştirilmesi ve plastik atıkların yeniden kullanımının artırılması açısından büyük potansiyele sahiptir. Bu sayede, daha temiz ve sağlıklı bir çevre için önemli adımlar atılabilir ve gelecek nesillere daha sürdürülebilir bir dünya bırakılabilir.
Plastik Enjeksiyon Yöntemlerine Genel Bir Giriş
Plastik enjeksiyon, endüstride en yaygın olarak kullanılan üretim yöntemlerinden biridir. Bu yöntem, polimer malzemelerin ısıtılıp eritilerek, bir enjeksiyon makinesi yardımıyla kalıplara enjekte edilerek ürünlerin üretildiği bir süreçtir. Plastik enjeksiyon yöntemi, çeşitli sektörlerde kullanılan çeşitli plastik parçaların üretimi için ideal bir yöntemdir.
Plastik enjeksiyon süreci, genel olarak dört adımdan oluşur: malzeme hazırlama, eritme, enjeksiyon ve soğutma. İlk adımda, plastik malzeme, uygun granül veya pellet formunda hazırlanır. Bu malzemeler, enjeksiyon makinesinin haznesine yerleştirilir ve malzemenin homojen bir şekilde erimesini sağlamak için ısıtılır. Malzeme eridikten sonra, enjeksiyon pistonuyla kalıba enjekte edilir. Enjeksiyon işlemi, malzemenin kalıp boşluğuna yüksek basınç altında pompalanmasını içerir. Enjeksiyon tamamlandıktan sonra, malzeme soğuması için bir süre bekletilir. Son adımda ise, kalıptan çıkan plastik parça çıkarılır ve gerektiğinde son işlemlere tabi tutulur.
Plastik enjeksiyon yöntemi, birçok avantaj sunar. Bu yöntemle, karmaşık şekillerde parçalar üretmek mümkündür. Kalıplar, çeşitli şekil ve boyutlarda tasarlanabilir ve bu sayede özelleştirilmiş parçalar elde edilebilir. Ayrıca, plastik enjeksiyon süreci, seri üretim için hızlı ve verimli bir yöntemdir. Üretim süreci otomatikleştirilebilir ve yüksek hassasiyetle tekrarlanabilir.
Plastik enjeksiyon yöntemi, otomotiv, elektronik, tüketici ürünleri, ambalaj, tıbbi ekipmanlar gibi birçok sektörde yaygın olarak kullanılmaktadır. Bu yöntemle üretilen plastik parçalar, hafif, dayanıklı, korozyona dirençli ve ekonomik avantajlar sunar. Ayrıca, plastik malzemelerin geri dönüşümü de mümkündür, bu da sürdürülebilirlik açısından önemli bir avantajdır.
Sonuç olarak, plastik enjeksiyon yöntemi, endüstride yaygın olarak kullanılan bir üretim yöntemidir. Bu yöntem, çeşitli sektörlerde kullanılan plastik parçaların hızlı, verimli ve özelleştirilebilir bir şekilde üretilmesini sağlar. Plastik enjeksiyon süreci, malzeme hazırlama, eritme, enjeksiyon ve soğutma adımlarından oluşur. Bu yöntem, karmaşık şekillerde parçaların üretimini mümkün kılar ve seri üretim için ideal bir seçenektir.
Plastik enjeksiyon yönteminin birçok avantajı vardır. İlk olarak, bu yöntemle yüksek kalitede ve hassas plastik parçalar üretilebilir. Kalıp tasarımı esnekliği sayesinde farklı şekillerde ve boyutlarda parçalar üretmek mümkündür. Bu, tasarımcılara ve mühendislere geniş bir yaratıcılık alanı sağlar.
Plastik enjeksiyon yöntemi ayrıca verimli bir üretim süreci sunar. Otomatik enjeksiyon makineleri, yüksek hızda ve sürekli olarak parçaların üretimini gerçekleştirebilir. Bu da seri üretim için zaman ve maliyet tasarrufu sağlar. Ayrıca, enjeksiyon sürecinin tekrarlanabilirliği yüksektir, bu da parçaların kalite ve hassasiyetini sağlar.
Plastik enjeksiyon yöntemi, çeşitli sektörlerde yaygın olarak kullanılmaktadır. Otomotiv endüstrisi, elektronik, tüketici ürünleri, ambalaj ve tıbbi ekipman gibi alanlarda enjeksiyonla üretilen plastik parçaların kullanımı yaygındır. Bu parçalar, hafif, dayanıklı ve korozyona dayanıklıdır. Aynı zamanda, plastik malzemelerin geri dönüşümü de mümkündür, bu da çevresel açıdan önemlidir.
Son yıllarda, plastik enjeksiyon yönteminde çeşitli yenilikler ve gelişmeler yaşanmaktadır. Malzeme teknolojilerindeki ilerlemeler, daha dayanıklı ve sürdürülebilir plastik malzemelerin kullanımını mümkün kılmıştır. Ayrıca, enjeksiyon makinelerindeki otomasyon ve dijitalleşme, üretim sürecini daha verimli hale getirmiştir.
Gelişen teknolojiler ve yenilikler, plastik enjeksiyon yöntemini daha da ileriye taşımaktadır. 3D baskı teknolojisi ile entegre edilen enjeksiyon makineleri, daha karmaşık tasarımların üretimini sağlamaktadır. Ayrıca, yenilikçi malzeme kombinasyonları ve geri dönüşümlü plastiklerin kullanımıyla çevresel etkiler daha da azaltılmaktadır.
Plastik enjeksiyon yöntemi, plastik parçaların hızlı, verimli ve yüksek kalitede üretimini sağlayan önemli bir teknolojidir. Yenilikler ve gelişmeler, bu yöntemi daha da etkili hale getirmekte ve daha geniş bir uygulama alanı sunmaktadır.
Birçok sektörde kullanılan plastik enjeksiyon yöntemi, otomotiv endüstrisinden tüketici ürünlerine, tıbbi ekipmandan elektronik bileşenlere kadar çeşitli ürünlerin üretiminde kullanılmaktadır. Bu yöntemle üretilen plastik parçalar, yüksek dayanıklılık, mukavemet ve işlevsellik sağlamaktadır. Ayrıca, tasarım esnekliği sayesinde farklı şekil ve boyutlarda parçalar üretmek mümkündür.
Son yıllarda, plastik enjeksiyon yönteminde çeşitli yenilikler ortaya çıkmıştır. Örneğin, hızlı enjeksiyon teknolojisi, enjeksiyon süresini kısaltarak üretim hızını artırmakta ve enerji verimliliğini iyileştirmektedir. Ayrıca, çok bileşenli enjeksiyon teknolojisi, farklı malzemelerin aynı parçada kullanılmasını sağlamaktadır. Bu da parçaların işlevselliğini artırırken, maliyeti ve üretim süresini azaltmaktadır.
Plastik enjeksiyon yöntemindeki bir diğer yenilik ise dijitalleşme ve otomasyon teknolojileridir. Gelişmiş enjeksiyon makineleri, dokunmatik ekran arayüzleri ve veri analitiği gibi özelliklerle donatılmıştır. Bu sayede üretim süreci daha kolay yönetilebilir ve izlenebilir hale gelmektedir. Ayrıca, robotik sistemlerin entegrasyonu, parça çıkarılması ve işleme operasyonlarını otomatikleştirmekte ve insan hatalarını en aza indirmektedir.
Sürdürülebilirlik, plastik enjeksiyon yöntemindeki yeniliklerin önemli bir odak noktasıdır. Geri dönüşümlü plastik malzemelerin kullanımı ve atık yönetimi stratejileri, çevresel etkileri azaltmak için önemli adımlardır. Ayrıca, biyobozunur ve yenilenebilir polimerlerin kullanımı da sürdürülebilirlik açısından büyük potansiyele sahiptir.
Sonuç olarak, plastik enjeksiyon yöntemi, endüstride yaygın olarak kullanılan ve sürekli gelişen bir üretim teknolojisidir. Yenilikler ve gelişmeler, daha hızlı, verimli ve çevre dostu üretim süreçleri sağlamaktadır. Plastik enjeksiyon yöntemi, geniş bir uygulama yelpazesine sahiptir ve sektörler arasında büyük bir öneme sahiptir. Bununla birlikte, gelecekte plastik enjeksiyon yöntemine yönelik daha fazla yenilik ve gelişme beklenmektedir. 3D baskı teknolojisinin enjeksiyon süreciyle birleştirilmesi, daha karmaşık ve özelleştirilmiş parçaların üretimini kolaylaştıracaktır. Malzeme teknolojilerindeki ilerlemeler, daha dayanıklı, hafif ve çevre dostu plastik malzemelerin kullanılmasını mümkün kılacaktır.
Ayrıca, yapay zeka ve otomasyon teknolojilerinin daha fazla entegrasyonu, üretim sürecini daha verimli ve hatasız hale getirecektir. Makine öğrenimi ve veri analitiği, enjeksiyon sürecinin optimize edilmesini sağlayacak ve üretim verimliliğini artıracaktır.
Sürdürülebilirlik açısından, geri dönüşüm teknolojilerinin geliştirilmesi ve daha fazla geri dönüştürülebilir plastik malzemenin kullanımı büyük önem taşımaktadır. Plastik atıklarının azaltılması ve yeniden kullanılabilirliğinin artırılması, çevresel etkileri azaltmada kritik bir rol oynayacaktır.
Ayrıca, biyobozunur ve yenilenebilir plastik malzemelerin kullanımıyla birlikte, plastik enjeksiyon yöntemi daha çevre dostu hale gelecektir. Bu tür malzemeler, doğal olarak parçalanabilir ve doğaya zarar vermeden yok olabilir.
Sonuç olarak, plastik enjeksiyon yöntemi, endüstrideki önemli bir üretim teknolojisi olmaya devam etmektedir. Yenilikler ve gelişmeler, daha hızlı, verimli, özelleştirilebilir ve çevre dostu üretim süreçlerini mümkün kılmaktadır. Plastik enjeksiyon yöntemi, sektörler arasında yaygın olarak kullanılan ve sürekli olarak geliştirilen bir teknolojidir ve gelecekte de önemini koruyacaktır.
Konvansiyonel Enjeksiyon Kalıplama: Çalışma Prensibi ve Uygulamaları
Konvansiyonel enjeksiyon kalıplama, plastik parçaların üretiminde en yaygın kullanılan yöntemlerden biridir. Bu yöntem, bir enjeksiyon presi ve bir enjeksiyon kalıbı kullanılarak gerçekleştirilir. Prensibi, plastik malzemenin eritilerek kalıba enjekte edilmesi ve soğutulmasıdır.
Çalışma prensibi şu şekildedir: İlk adım olarak, kalıp hazırlanır. Kalıp, istenen plastik parçanın şekline uygun olarak tasarlanır ve üretim için uygun malzemeyle kaplanır. Kalıp, iki veya daha fazla parçadan oluşabilir ve enjeksiyon presine monte edilir.
İkinci adımda, plastik malzeme hazırlanır. Plastik granüller, bir huni veya otomatik besleme sistemi aracılığıyla enjeksiyon presine aktarılır. Bu granüller, presin içerisindeki bir vida veya piston tarafından itilerek eritme bölgesine taşınır.
Üçüncü adımda, plastik malzeme eritilir. Vida veya piston tarafından itilen granüller, ısıtılan silindir içerisinde eritilir. Bu sıcak erimiş plastik, homojen bir şekilde karıştırılır ve enjeksiyon basıncı altında kalıba doğru ilerletilir.
Dördüncü adımda, plastik malzeme enjeksiyon kalıbına enjekte edilir. Presin hidrolik veya mekanik sistemleri kullanılarak, erimiş plastik malzeme yüksek basınç altında kalıba enjekte edilir. Enjeksiyon sırasında malzeme, kalıp boşluğunu tamamen dolduracak şekilde kontrollü bir şekilde ilerler.
Beşinci adımda, plastik malzeme soğutulur. Enjeksiyon tamamlandıktan sonra, kalıp içerisindeki plastik parça soğuması için bırakılır. Soğutma süresi, plastik parçanın boyutuna, kalıp tasarımına ve kullanılan malzemeye bağlı olarak değişir.
Altıncı ve son adımda, plastik parça çıkarılır ve kalıp hazırlanır. Kalıp açılarak, plastik parça dikkatlice çıkarılır. Parça, kalıp üzerinde oluşan artıklardan temizlenir ve kalıp tekrar kullanıma hazır hale getirilir.
Konvansiyonel enjeksiyon kalıplama yöntemi, geniş bir uygulama yelpazesine sahiptir. Otomotiv sektöründe, tüketici ürünlerinde, elektronik ekipmanlarda, ambalaj malzemelerinde ve daha birçok alanda kullanılmaktadır. Bu yöntemle üretilen plastik parçalar, yüksek kalite, hassasiyet ve tekrarlanabilirlik sağlar. Ayrıca, karmaşık geometrilerin ve ince duvarlı parçaların üretimi için uygundur.
Konvansiyonel enjeksiyon kalıplama yönteminin birçok avantajı vardır. İlk olarak, yüksek hacimli üretim için hızlı ve verimli bir yöntemdir. Kalıp tasarımının optimize edilmesiyle, aynı anda birden fazla parçanın üretimi mümkün olabilir. Bu da üretim verimliliğini artırır ve maliyetleri düşürür.
İkinci olarak, konvansiyonel enjeksiyon kalıplama yöntemi, çeşitli plastik malzemelerin kullanımına olanak tanır. Termoplastik malzemeler, termoset malzemeler ve elastomerler gibi farklı plastik türleri bu yöntemle işlenebilir. Bu da çeşitlilik ve esneklik sağlar ve farklı uygulama gereksinimlerini karşılar.
Ayrıca, kalıp tasarımında değişiklik yaparak, farklı parça geometrileri ve özellikleri elde etmek mümkündür. Özelleştirilmiş kalıplar kullanılarak, farklı şekillerde oyuklar, kesişimler, delikler ve girinti çıkıntılar oluşturulabilir. Böylece, tasarım esnekliği ve işlevsellik artar.
Konvansiyonel enjeksiyon kalıplama yöntemi aynı zamanda kalite ve hassasiyet açısından da avantaj sağlar. Kalıp içerisindeki plastik malzeme, yüksek basınç ve sıcaklık altında homojen bir şekilde dağılır. Bu, parçaların istenilen boyut, şekil ve yüzey kalitesine sahip olmasını sağlar. Ayrıca, kalıp tasarımında hassas toleranslar sağlanabilir.
Ancak, konvansiyonel enjeksiyon kalıplama yönteminin bazı sınırlamaları da vardır. Kalıp hazırlama süreci karmaşık olabilir ve uzun sürebilir. Ayrıca, yüksek maliyetli kalıpların tasarlanması ve üretimi gerekebilir. Bu nedenle, küçük ölçekli üretimlerde veya özelleştirilmiş parçaların üretiminde maliyet etkili olmayabilir.
Sonuç olarak, konvansiyonel enjeksiyon kalıplama yöntemi, plastik parçaların seri üretimi için yaygın olarak kullanılan bir teknolojidir. Yüksek verimlilik, kalite, esneklik ve tasarım özgürlüğü sağlar. Ancak, her uygulamada uygun olmayabilir ve maliyet faktörleri
göz önünde bulundurulmalıdır. Özellikle küçük ölçekli üretimlerde veya özelleştirilmiş parçaların üretiminde, diğer üretim yöntemleri daha uygun olabilir.
Bununla birlikte, konvansiyonel enjeksiyon kalıplama yönteminin sürekli olarak geliştirildiği ve yeniliklerin yapıldığı unutulmamalıdır. Örneğin, hızlı kalıp değiştirme sistemleri ve otomasyon teknolojileri, üretim süreçlerini daha verimli ve esnek hale getirmektedir. Ayrıca, malzeme teknolojilerindeki ilerlemeler, daha dayanıklı, hafif ve çevre dostu plastik malzemelerin kullanılmasını sağlamaktadır.
Sonuç olarak, konvansiyonel enjeksiyon kalıplama yöntemi, plastik parça üretimi için güvenilir, yaygın ve etkili bir yöntemdir. Yüksek hacimli üretimlerde, kalite ve hassasiyet gerektiren uygulamalarda ve standart geometrilere sahip parçaların üretiminde tercih edilmektedir. Ancak, her uygulama için en uygun üretim yönteminin belirlenmesi için dikkatli bir değerlendirme yapılmalı ve yeniliklere açık olunmalıdır.
Mikro Enjeksiyon Kalıplama: Hassas ve Küçük Parçalar
Mikro enjeksiyon kalıplama, plastik parçaların çok küçük boyutlarda ve yüksek hassasiyetle üretimi için özel olarak tasarlanmış bir enjeksiyon kalıplama yöntemidir. Bu yöntem, genellikle mikroelektronik, tıbbi cihazlar, telekomünikasyon ve otomotiv gibi alanlarda kullanılan hassas ve küçük parçaların üretimi için tercih edilir.
Mikro enjeksiyon kalıplama süreci, konvansiyonel enjeksiyon kalıplama yöntemine benzer şekilde ilerler, ancak daha küçük ölçekte gerçekleştirilir. İşlem adımları şunlardır:
- Kalıp Hazırlığı: İlk adımda, mikro enjeksiyon kalıplama için özel olarak tasarlanmış bir kalıp hazırlanır. Kalıp, çok küçük ve hassas parçaların şekline uygun olarak üretilir. Kalıp malzemesi genellikle sertleştirilmiş çelik veya özel alaşımlardan oluşur.
- Malzeme Hazırlığı: Mikro enjeksiyon kalıplama için kullanılacak plastik malzeme, granül veya toz formunda hazırlanır. Malzeme seçimi, parçanın özelliklerine ve uygulamaya bağlı olarak yapılır. Yüksek performans gerektiren uygulamalarda, teknik plastikler veya özel kompozit malzemeler kullanılabilir.
- Enjeksiyon Süreci: Malzeme hazırlık aşamasından sonra, enjeksiyon presi kullanılarak malzeme eritilir ve enjeksiyon odasına aktarılır. Mikro enjeksiyon kalıplama için özel olarak tasarlanmış bir enjeksiyon ünitesi kullanılır. Malzeme, yüksek basınç altında kalıp boşluğuna enjekte edilir ve parça şeklini alır.
- Soğutma: Enjeksiyon tamamlandıktan sonra, plastik parça kalıp içerisinde soğutulur. Bu aşama, parçanın boyutuna ve malzeme özelliklerine bağlı olarak değişebilir. Soğutma süresi, parçanın istenen boyut, şekil ve kaliteye ulaşması için önemlidir.
- Parça Çıkarma: Parça tamamen soğuduktan sonra, kalıp açılarak parça çıkarılır. Mikro enjeksiyon kalıplama işlemi, küçük ve hassas parçaların üretimi için özel olarak tasarlanmış bir çekme sistemi kullanır. Parçanın hassas şeklinin korunmasını sağlar ve hasar riskini en aza indirir.
Mikro enjeksiyon kalıplama yöntemi, çok küçük ve yüksek hassasiyet gerektiren parçaların üretiminde avantajlıdır. Bu yöntem, genellikle milimetrenin altında boyutlara sahip parçaların üretiminde kullanılır. Örneğin, mikro dişliler, mikro tüpler, mikro konektörler gibi parçalar mikro enjeksiyon kalıplama ile üretilebilir.
Mikro enjeksiyon kalıplama yönteminin bazı avantajları vardır. İlk olarak, yüksek hassasiyet sağlar. Mikro enjeksiyon kalıplama, çok küçük boyutlardaki parçaların üretiminde bile ±0.001 mm’ye kadar hassasiyet sağlayabilir. Bu, parçaların doğru ve tutarlı boyutlarda üretilmesini sağlar.
İkinci olarak, mikro enjeksiyon kalıplama yöntemi, malzeme verimliliği açısından avantajlıdır. Küçük boyutlardaki parçalar için gereken malzeme miktarı oldukça düşüktür. Bu da malzeme maliyetlerini düşürür ve sürdürülebilirlik açısından önemli bir faktördür.
Ayrıca, mikro enjeksiyon kalıplama yöntemi, karmaşık geometrili parçaların üretimini mümkün kılar. Mikro boyutlardaki parçaların üretiminde bile karmaşık şekiller, girinti-çıkıntılar ve ince detaylar elde edilebilir. Bu, tasarım özgürlüğünü artırır ve farklı uygulama gereksinimlerini karşılar.
Mikro enjeksiyon kalıplama yöntemi, birçok sektörde çeşitli uygulamalara sahiptir. Örneğin, tıbbi cihaz endüstrisinde, mikro iğneler, mikro valfler, mikro enjektörler gibi parçaların üretiminde kullanılır. Elektronik endüstrisinde, mikro konektörler, mikro sensörler ve mikro bileşenlerin üretiminde önemli bir rol oynar. Ayrıca otomotiv, telekomünikasyon, optik ve savunma gibi birçok sektörde de mikro enjeksiyon kalıplama yöntemi kullanılır.
Ancak, mikro enjeksiyon kalıplama yöntemi bazı zorlukları da beraberinde getirir. Kalıp tasarımı ve üretimi oldukça karmaşık olabilir. Ayrıca, yüksek hassasiyet gerektiren işlemler, deneyimli operatörler ve özel ekipmanlar gerektirebilir. Bu nedenle, mikro enjeksiyon kalıplama işlemi, uzmanlık ve dikkat gerektiren bir yöntemdir.
Sonuç olarak, mikro enjeksiyon kalıplama yöntemi, hassas ve küçük boyutlardaki parçaların üretimi için etkili ve uygun bir yöntemdir. Yüksek hassasiyet, malzeme verimliliği ve karmaşık geometrilerin elde edilebilmesi, mikro enjeksiyon kalıplamanın önemli avantajları arasında yer almaktadır. Bu yöntem, tıbbi, elektronik, otomotiv ve diğer endüstrilerde geniş bir uygulama alanı bulmaktadır.
Multi-Materyal Enjeksiyon Kalıplama: Çoklu Bileşenli Ürünler;
Multi-materyal enjeksiyon kalıplama, farklı malzemelerin aynı enjeksiyon kalıbında birleştirilerek çoklu bileşenli ürünlerin üretimini sağlayan bir yöntemdir. Bu yöntem, farklı malzemelerin özelliklerini birleştirerek daha karmaşık ve fonksiyonel parçaların elde edilmesini mümkün kılar. Multi-materyal enjeksiyon kalıplama, otomotiv, elektronik, tıbbi cihazlar ve ev aletleri gibi çeşitli endüstrilerde yaygın olarak kullanılan bir teknolojidir.
Multi-materyal enjeksiyon kalıplama süreci, aşağıdaki adımları içerir:
Tasarım ve Malzeme Seçimi: İlk adımda, çoklu bileşenli parçaların tasarımı yapılır ve kullanılacak malzemeler seçilir. Farklı malzemelerin uyumlu olması ve kalıp üzerinde iyi bir bağlantı sağlaması önemlidir. Malzeme seçimi, parçanın işlevine, mukavemet gereksinimlerine ve görünüme bağlı olarak yapılır.
Kalıp Hazırlığı: Multi-materyal enjeksiyon kalıplama için özel olarak tasarlanmış bir kalıp hazırlanır. Kalıp, farklı malzemelerin enjeksiyon bölümlerini içeren birden fazla bölmeden oluşur. Her bir bileşen için ayrı bir malzeme enjeksiyon noktası bulunur.
Malzeme Hazırlığı ve Enjeksiyon: Her bir bileşen için ayrı malzemeler hazırlanır ve enjeksiyon presine yerleştirilir. Enjeksiyon süreci sırasında, malzemeler sırasıyla enjeksiyon noktalarına gönderilir ve kalıp içindeki boşluklara doldurulur. Malzemeler birbirleriyle birleşir ve istenen bileşenlerin oluşmasını sağlar.
Soğutma ve Çıkarma: Enjeksiyon tamamlandıktan sonra, parçalar kalıp içinde soğutulur. Her bir bileşenin farklı malzeme özelliklerine bağlı olarak soğuma süreleri değişebilir. Soğutma sürecinden sonra, parçalar çıkarılır ve istenen boyut, şekil ve kaliteye sahip olur.
Multi-materyal enjeksiyon kalıplama yöntemi, çeşitli avantajlara sahiptir. İlk olarak, daha karmaşık ve fonksiyonel parçaların üretilmesini sağlar. Farklı malzemelerin kombinasyonu, parçaların özelliklerini iyileştirir ve daha çeşitli işlevlere sahip ürünlerin ortaya çıkmasını sağlar. Örneğin, bir otomobil içerisinde plastik ve kauçuk bileşenlerin bir arada kullanılması, dayanıklılığı artırırken titreşimi azaltabilir.
İkinci olarak, maliyet ve üretim süresi açısından avantajlıdır. Multi-materyal enjeksiyon kalıplama, birden fazla bileşeni aynı kalıpta üretme imkanı sağladığından, ayrı kalıpların kullanılması ve ayrı enjeksiyon işlemlerinin gerçekleştirilmesine göre daha ekonomiktir. Ayrıca, üretim süresini kısaltarak seri üretim için daha verimli bir seçenektir.
Ayrıca, multi-materyal enjeksiyon kalıplama yöntemi, tasarım özgürlüğünü artırır. Farklı malzemelerin birleştirilmesi, parçaların daha karmaşık geometrilerde tasarlanabilmesini sağlar. Örneğin, bir plastik gövde üzerine elastik bir contanın enjekte edilmesiyle, sızdırmazlık ve darbe emilimi gibi özelliklerin bir arada sağlanması mümkündür.
Bununla birlikte, multi-materyal enjeksiyon kalıplama yöntemi bazı zorlukları da beraberinde getirir. Malzemelerin uyumlu olması ve kalıp üzerinde iyi bir bağlantı sağlaması önemlidir. Malzemelerin farklı termal genleşme katsayılarına sahip olması ve yapışma problemleri gibi sorunlarla karşılaşılabilir. Bu nedenle, kalıp tasarımı ve malzeme seçimi konusunda dikkatli ve detaylı bir çalışma gerekmektedir.
Sonuç olarak, multi-materyal enjeksiyon kalıplama yöntemi, farklı malzemelerin bir arada kullanılmasıyla daha karmaşık ve fonksiyonel parçaların üretimini sağlayan bir teknolojidir. Avantajları arasında karmaşık tasarım imkanı, maliyet ve üretim süresinde tasarruf sağlama ve işlevselliği artırma bulunmaktadır. Ancak, malzeme uyumu ve kalıp tasarımı gibi zorlukları göz önünde bulundurarak, doğru yöntem ve uygun malzemelerin seçilmesi önemlidir.